OxVent: could this prototype ventilator save thousands of lives?
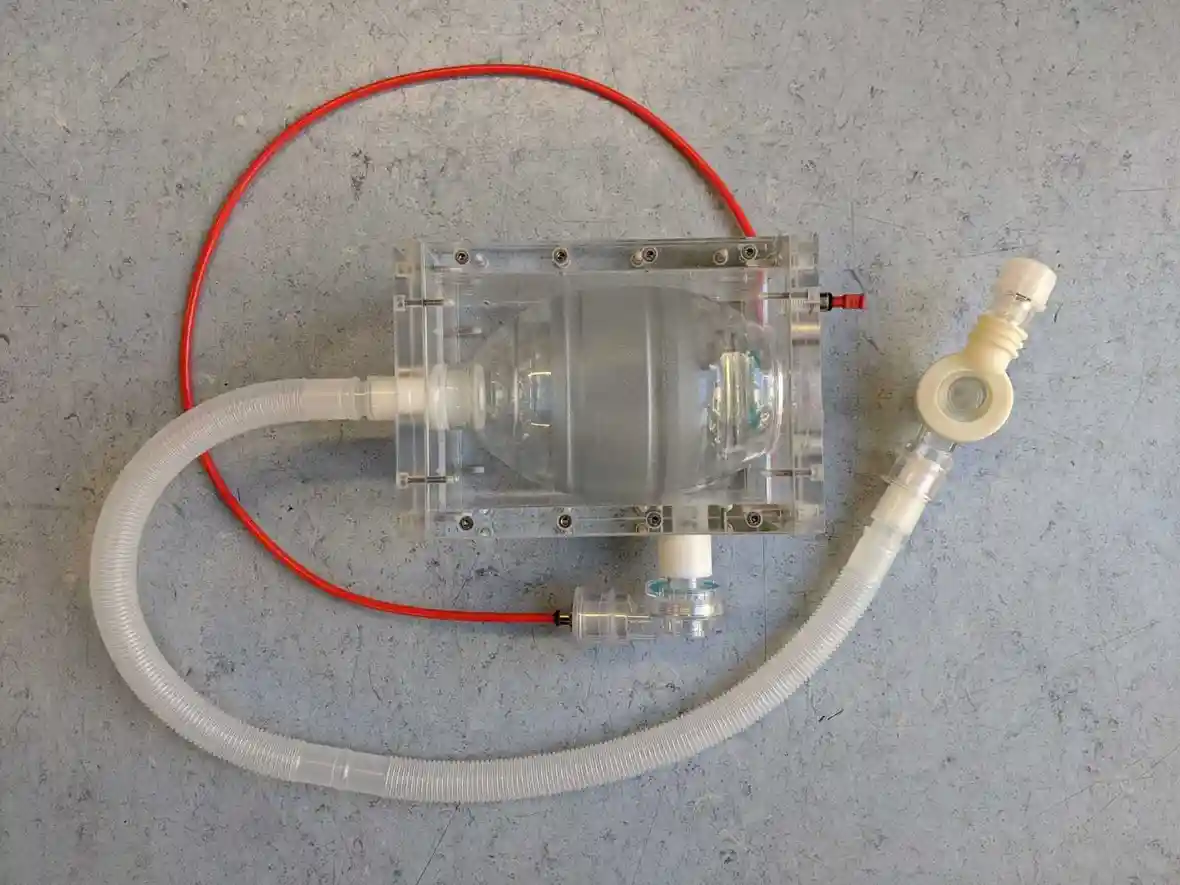
Meet the mega-brain engineers, clinicians, students and manufacturers from Oxford University and King’s College who have built a machine that could be key to the battle against COVID-19.
Life
Words: Chris Stokel-Walker
In just one week, a team at Oxford University and King’s College London have built a simple ventilator that could potentially save thousands of lives as part of the UK and the world’s fight against coronavirus. The OxVent is a rapid prototype ventilator that could keep people breathing while they battle the worst impacts of COVID-19. Andrew Farmery of the University of Oxford, one of the people involved in its development, talks about its past, present, and potential.
How are you?
I’m very well, although slightly knackered. It’s been a very long week. It’s been absolutely incredible, from nothing a week ago when we first had an idle chat Monday morning last week, to this afternoon, when we pitched it to the Cabinet and the MHRA (Medicines and Healthcare Products Regulatory Agency). We’re waiting to hear whether they think it’s a goer or not.
It’s been phenomenal, just going through several different designs and prototyping, involving all the different people, engineers, regulation experts. It’s been an amazing collaboration between my colleagues at Oxford and also King’s and all sorts of people just phoning up and offering to take on tasks and get all the documentation together, which is about as tall as I am. Now we’re just waiting for the call from the Cabinet Office.
What questions were they asking?
As well as an academic, I’m also a consultant anaesthetist, so I deal with ventilating patients every week. That’s what I do. The design had come out of what the clinicians want. We were slightly worried at the start when Boris announced Land Rover and JCB were going to be making ventilators. I was slightly alarmed that they knew sod-all about ventilators and nobody had really taken the opinions of people like me and doctors and anaesthetists around the country.
The MHRA specification was quite high and we simply don’t need anything that complicated or high-spec. We just need a basic bit of kit that gets the job done and saves lives, and we need it within two weeks otherwise the body count will be huge.
-
“It’s laughably simple in some ways. It’s a compressible bag, a bit like a child’s rugby ball.” “It’s laughably simple in some ways. It’s a compressible bag, a bit like a child’s rugby ball.” “It’s laughably simple in some ways. It’s a compressible bag, a bit like a child’s rugby ball.” “It’s laughably simple in some ways. It’s a compressible bag, a bit like a child’s rugby ball.” “It’s laughably simple in some ways. It’s a compressible bag, a bit like a child’s rugby ball.” “It’s laughably simple in some ways. It’s a compressible bag, a bit like a child’s rugby ball.” “It’s laughably simple in some ways. It’s a compressible bag, a bit like a child’s rugby ball.” “It’s laughably simple in some ways. It’s a compressible bag, a bit like a child’s rugby ball.” “It’s laughably simple in some ways. It’s a compressible bag, a bit like a child’s rugby ball.” “It’s laughably simple in some ways. It’s a compressible bag, a bit like a child’s rugby ball.” “It’s laughably simple in some ways. It’s a compressible bag, a bit like a child’s rugby ball.” “It’s laughably simple in some ways. It’s a compressible bag, a bit like a child’s rugby ball.” “It’s laughably simple in some ways. It’s a compressible bag, a bit like a child’s rugby ball.” “It’s laughably simple in some ways. It’s a compressible bag, a bit like a child’s rugby ball.” “It’s laughably simple in some ways. It’s a compressible bag, a bit like a child’s rugby ball.” “It’s laughably simple in some ways. It’s a compressible bag, a bit like a child’s rugby ball.” “It’s laughably simple in some ways. It’s a compressible bag, a bit like a child’s rugby ball.” “It’s laughably simple in some ways. It’s a compressible bag, a bit like a child’s rugby ball.” “It’s laughably simple in some ways. It’s a compressible bag, a bit like a child’s rugby ball.” “It’s laughably simple in some ways. It’s a compressible bag, a bit like a child’s rugby ball.” “It’s laughably simple in some ways. It’s a compressible bag, a bit like a child’s rugby ball.” “It’s laughably simple in some ways. It’s a compressible bag, a bit like a child’s rugby ball.” “It’s laughably simple in some ways. It’s a compressible bag, a bit like a child’s rugby ball.” “It’s laughably simple in some ways. It’s a compressible bag, a bit like a child’s rugby ball.” “It’s laughably simple in some ways. It’s a compressible bag, a bit like a child’s rugby ball.” “It’s laughably simple in some ways. It’s a compressible bag, a bit like a child’s rugby ball.” “It’s laughably simple in some ways. It’s a compressible bag, a bit like a child’s rugby ball.” “It’s laughably simple in some ways. It’s a compressible bag, a bit like a child’s rugby ball.” “It’s laughably simple in some ways. It’s a compressible bag, a bit like a child’s rugby ball.” “It’s laughably simple in some ways. It’s a compressible bag, a bit like a child’s rugby ball.” “It’s laughably simple in some ways. It’s a compressible bag, a bit like a child’s rugby ball.” “It’s laughably simple in some ways. It’s a compressible bag, a bit like a child’s rugby ball.” “It’s laughably simple in some ways. It’s a compressible bag, a bit like a child’s rugby ball.” “It’s laughably simple in some ways. It’s a compressible bag, a bit like a child’s rugby ball.” “It’s laughably simple in some ways. It’s a compressible bag, a bit like a child’s rugby ball.” “It’s laughably simple in some ways. It’s a compressible bag, a bit like a child’s rugby ball.” “It’s laughably simple in some ways. It’s a compressible bag, a bit like a child’s rugby ball.” “It’s laughably simple in some ways. It’s a compressible bag, a bit like a child’s rugby ball.” “It’s laughably simple in some ways. It’s a compressible bag, a bit like a child’s rugby ball.” “It’s laughably simple in some ways. It’s a compressible bag, a bit like a child’s rugby ball.”
How many parts are there in this, and how long has it taken to iterate?
It’s laughably simple in some ways. It’s a compressible bag, a bit like a child’s rugby ball. It’s a compressible squeezy bag – the sort you use to resuscitate patients who have collapsed from cardiac arrest. Ambulances carry them around. But we’ve trapped it inside a rigid Perspex box and we inject compressed air into the rigid Perspex box that squeezes this bladder and pushes air out through some valves which we already have, and inflates the patient’s chest. There’s a second set of valves that allows gas to come out of the patient’s chest and also out of the rigid Perspex box. So it’s a sort of electro-pneumatic device.
The air is injected into the box through what’s called a solenoid valve, which is controlled electronically, and we can regulate the flow of air compression gas that goes into the box, the speed with which it goes in, how much time is allowed for inspiration and expiration. We can control the pressures generated in the patient’s airway. All the things you would want, and we’re just doing it with this simple feedback controller.
The electronics is based around a very simple circuit board called an Arduino – basically a tiny little circuit board used to teach kids about coding and electronics. It’s basically a toy, but that’s what the prototype is based on. We might even base the whole thing on that. It depends on whether we can knock PCBs out quickly enough. So the control engineers are still working on that, refining it. You’ve got to tell the solenoid valve what to do and then you’ve got to measure and monitor the pressures at various points with sensors to make sure that the solenoid is doing what you told it to do. That’s classic control engineering and they love that sort of thing, and they’re off on it already.
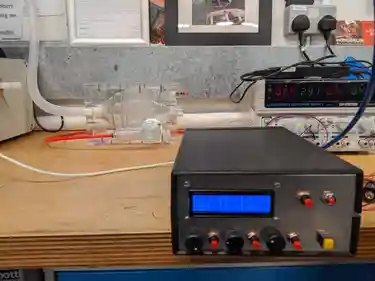
So how is this different from a standard medical ventilator?
Well there are two kinds of ventilators: the basic model we use in the operating theatre, because patients aren’t generally that sick, or at least their lungs aren’t that sick. Then there are some very sophisticated ones on the ICUs with lots of different knobs and twiddly bits in. But they are very sophisticated, very expensive, and in very short supply. You simply can’t knock them out rapidly.
You can’t even knock out the ones in the operating theatres rapidly because there’s 200 parts in them and lots of moving parts that need to be machined and tooled and you simply can’t upscale the production rapidly enough.
The difference in our system is it uses the same basic principle that is used in a fairly simple operating theatre ventilator, but it doesn’t use any of the same components. It has basically repurposed all sorts of different components that are already in the NHS supply chain – bits of tubing for this, breathing valves for that and bags for this and the other. None of them are ordinarily used to make a ventilator. We were mindful of the fact that supply chains would be absolutely at a standstill so we couldn’t say: “I want a three-eights, 20cm water pop off valve machined and built with this thread,” because we simply wouldn’t get it.
We went through the supply chain looking for bits that were designed for some other purpose in the NHS and were on the shelves. The whole design strategy was simplicity: very few moving parts, and very few parts at all. It needs to be cheap – it’s probably less than £1,000 – and could be put together by anybody, really. For quality control purposes we’re probably going to restrict it to ISO-certified fabricators, but literally a 16-year-old could do it in their bedroom.
There are some control electronics which are a bit more complex, but we’re burning that into chips and producing a schematic for a printed circuit board (PCB). We’ve had lots of offers from Sony, who have a big PCB factory in Bridgend that stopped production and could make them, and quite a few other PCB people who have offered to knock these circuit boards out.
We can get the electronics done pretty quick and we can get the assembly done because it’s so simple. We think we can get – it’s difficult to say, these are all guesstimates – but we think 5,000 in a week, depending on how many people we can get to help.
-
“It’s a simple, IKEA-type ventilator. We could supply people with a box of parts and say: ‘Just assemble it.’” “It’s a simple, IKEA-type ventilator. We could supply people with a box of parts and say: ‘Just assemble it.’” “It’s a simple, IKEA-type ventilator. We could supply people with a box of parts and say: ‘Just assemble it.’” “It’s a simple, IKEA-type ventilator. We could supply people with a box of parts and say: ‘Just assemble it.’” “It’s a simple, IKEA-type ventilator. We could supply people with a box of parts and say: ‘Just assemble it.’” “It’s a simple, IKEA-type ventilator. We could supply people with a box of parts and say: ‘Just assemble it.’” “It’s a simple, IKEA-type ventilator. We could supply people with a box of parts and say: ‘Just assemble it.’” “It’s a simple, IKEA-type ventilator. We could supply people with a box of parts and say: ‘Just assemble it.’” “It’s a simple, IKEA-type ventilator. We could supply people with a box of parts and say: ‘Just assemble it.’” “It’s a simple, IKEA-type ventilator. We could supply people with a box of parts and say: ‘Just assemble it.’” “It’s a simple, IKEA-type ventilator. We could supply people with a box of parts and say: ‘Just assemble it.’” “It’s a simple, IKEA-type ventilator. We could supply people with a box of parts and say: ‘Just assemble it.’” “It’s a simple, IKEA-type ventilator. We could supply people with a box of parts and say: ‘Just assemble it.’” “It’s a simple, IKEA-type ventilator. We could supply people with a box of parts and say: ‘Just assemble it.’” “It’s a simple, IKEA-type ventilator. We could supply people with a box of parts and say: ‘Just assemble it.’” “It’s a simple, IKEA-type ventilator. We could supply people with a box of parts and say: ‘Just assemble it.’” “It’s a simple, IKEA-type ventilator. We could supply people with a box of parts and say: ‘Just assemble it.’” “It’s a simple, IKEA-type ventilator. We could supply people with a box of parts and say: ‘Just assemble it.’” “It’s a simple, IKEA-type ventilator. We could supply people with a box of parts and say: ‘Just assemble it.’” “It’s a simple, IKEA-type ventilator. We could supply people with a box of parts and say: ‘Just assemble it.’” “It’s a simple, IKEA-type ventilator. We could supply people with a box of parts and say: ‘Just assemble it.’” “It’s a simple, IKEA-type ventilator. We could supply people with a box of parts and say: ‘Just assemble it.’” “It’s a simple, IKEA-type ventilator. We could supply people with a box of parts and say: ‘Just assemble it.’” “It’s a simple, IKEA-type ventilator. We could supply people with a box of parts and say: ‘Just assemble it.’” “It’s a simple, IKEA-type ventilator. We could supply people with a box of parts and say: ‘Just assemble it.’” “It’s a simple, IKEA-type ventilator. We could supply people with a box of parts and say: ‘Just assemble it.’” “It’s a simple, IKEA-type ventilator. We could supply people with a box of parts and say: ‘Just assemble it.’” “It’s a simple, IKEA-type ventilator. We could supply people with a box of parts and say: ‘Just assemble it.’” “It’s a simple, IKEA-type ventilator. We could supply people with a box of parts and say: ‘Just assemble it.’” “It’s a simple, IKEA-type ventilator. We could supply people with a box of parts and say: ‘Just assemble it.’” “It’s a simple, IKEA-type ventilator. We could supply people with a box of parts and say: ‘Just assemble it.’” “It’s a simple, IKEA-type ventilator. We could supply people with a box of parts and say: ‘Just assemble it.’” “It’s a simple, IKEA-type ventilator. We could supply people with a box of parts and say: ‘Just assemble it.’” “It’s a simple, IKEA-type ventilator. We could supply people with a box of parts and say: ‘Just assemble it.’” “It’s a simple, IKEA-type ventilator. We could supply people with a box of parts and say: ‘Just assemble it.’” “It’s a simple, IKEA-type ventilator. We could supply people with a box of parts and say: ‘Just assemble it.’” “It’s a simple, IKEA-type ventilator. We could supply people with a box of parts and say: ‘Just assemble it.’” “It’s a simple, IKEA-type ventilator. We could supply people with a box of parts and say: ‘Just assemble it.’” “It’s a simple, IKEA-type ventilator. We could supply people with a box of parts and say: ‘Just assemble it.’” “It’s a simple, IKEA-type ventilator. We could supply people with a box of parts and say: ‘Just assemble it.’”
It’s across multiple universities: how many people are working on this?
It started off last Monday with just an idle comment by one of our PhD students at coffee, saying: “Blimey, we’re an engineering department: should we be doing something about this?” His supervisor, Mark Edwards, gave me a call. I’m the professor of anaesthetics in Oxford, so he thought I might be someone who knows something about it, and my research is in respiratory physiology, so it’s in my sort of area.
I first of all thought this is going to be too complicated. It’s going to be too difficult to get regulation. He said: “Just do it, let’s have a go.” Then I spoke to another colleague of mine, Federico Formenti at King’s College, and asked him if he wanted to join in.
I knew some good engineering contacts at King’s he may also be able to put us in touch with, and there’s another engineer called Alfonso Castrejon-Pita. There are four of us: myself, Mark Edwards, Alfonso and Federico. And all of our students. We basically said: “Look, put down your projects, put the PhDs on hold for a week, and come and muck in.” When the word got out, everybody was round the lab, everybody was wanting to do something. There were people phoning us up saying, “I know all about regulatory authority stuff. Can I work on the documentation for you?” We said: “Yeah, get on with it.”
Electronics people came and said: “You’ll need a feedback controller to control all the air injected in this. Can we get on with that?” We said: “Yeah, get on with it.” And it got to the point where my phone was buzzing every two minutes from people offering help. It became difficult to keep up.
By the time it had got out into the Twittersphere, various people were phoning us up and saying: “I run a light industrial fabrication plant in Coventry or wherever. Whatever you need, milling, 3D printing, tell me and we’ll do it.” So it’s just gone crazy like that. It’s got to the point where we need someone to go back through all our old emails and pick out all these people and co-ordinate it so we can fabricate it.
-
“If we just relied on conventional ventilator design, there’d be a huge number of deaths before they’re delivered.” “If we just relied on conventional ventilator design, there’d be a huge number of deaths before they’re delivered.” “If we just relied on conventional ventilator design, there’d be a huge number of deaths before they’re delivered.” “If we just relied on conventional ventilator design, there’d be a huge number of deaths before they’re delivered.” “If we just relied on conventional ventilator design, there’d be a huge number of deaths before they’re delivered.” “If we just relied on conventional ventilator design, there’d be a huge number of deaths before they’re delivered.” “If we just relied on conventional ventilator design, there’d be a huge number of deaths before they’re delivered.” “If we just relied on conventional ventilator design, there’d be a huge number of deaths before they’re delivered.” “If we just relied on conventional ventilator design, there’d be a huge number of deaths before they’re delivered.” “If we just relied on conventional ventilator design, there’d be a huge number of deaths before they’re delivered.” “If we just relied on conventional ventilator design, there’d be a huge number of deaths before they’re delivered.” “If we just relied on conventional ventilator design, there’d be a huge number of deaths before they’re delivered.” “If we just relied on conventional ventilator design, there’d be a huge number of deaths before they’re delivered.” “If we just relied on conventional ventilator design, there’d be a huge number of deaths before they’re delivered.” “If we just relied on conventional ventilator design, there’d be a huge number of deaths before they’re delivered.” “If we just relied on conventional ventilator design, there’d be a huge number of deaths before they’re delivered.” “If we just relied on conventional ventilator design, there’d be a huge number of deaths before they’re delivered.” “If we just relied on conventional ventilator design, there’d be a huge number of deaths before they’re delivered.” “If we just relied on conventional ventilator design, there’d be a huge number of deaths before they’re delivered.” “If we just relied on conventional ventilator design, there’d be a huge number of deaths before they’re delivered.” “If we just relied on conventional ventilator design, there’d be a huge number of deaths before they’re delivered.” “If we just relied on conventional ventilator design, there’d be a huge number of deaths before they’re delivered.” “If we just relied on conventional ventilator design, there’d be a huge number of deaths before they’re delivered.” “If we just relied on conventional ventilator design, there’d be a huge number of deaths before they’re delivered.” “If we just relied on conventional ventilator design, there’d be a huge number of deaths before they’re delivered.” “If we just relied on conventional ventilator design, there’d be a huge number of deaths before they’re delivered.” “If we just relied on conventional ventilator design, there’d be a huge number of deaths before they’re delivered.” “If we just relied on conventional ventilator design, there’d be a huge number of deaths before they’re delivered.” “If we just relied on conventional ventilator design, there’d be a huge number of deaths before they’re delivered.” “If we just relied on conventional ventilator design, there’d be a huge number of deaths before they’re delivered.” “If we just relied on conventional ventilator design, there’d be a huge number of deaths before they’re delivered.” “If we just relied on conventional ventilator design, there’d be a huge number of deaths before they’re delivered.” “If we just relied on conventional ventilator design, there’d be a huge number of deaths before they’re delivered.” “If we just relied on conventional ventilator design, there’d be a huge number of deaths before they’re delivered.” “If we just relied on conventional ventilator design, there’d be a huge number of deaths before they’re delivered.” “If we just relied on conventional ventilator design, there’d be a huge number of deaths before they’re delivered.” “If we just relied on conventional ventilator design, there’d be a huge number of deaths before they’re delivered.” “If we just relied on conventional ventilator design, there’d be a huge number of deaths before they’re delivered.” “If we just relied on conventional ventilator design, there’d be a huge number of deaths before they’re delivered.” “If we just relied on conventional ventilator design, there’d be a huge number of deaths before they’re delivered.”
Because I guess once all those people are corralled in, it could be even more, the production.
Yes. We’ve got this within a week without really asking, so if it’s co-ordinated and HM government puts its weight behind it, I think it could just be massive. It’s a simple, IKEA-type ventilator. We could supply people with a box of parts and say: “Just assemble it.”
So how much have you slept over the last week, Andrew?
Not much. Not much. When we got the electronics working at about 4:30am on Sunday morning, we were sort of too elated to go to bed, because we saw the lungs: we’ve got a dummy patient with lungs that you can see in their chest and we were twiddling the knobs and you could alter the size of the breath, pressure in the breath, the inspired/expired time ratio. All the things you could want to control, we were just twiddling with the knobs, watching it. It was extraordinary. So anyway, we had this pitch at 1:30pm and this afternoon was the first break we’ve had since we started last Monday morning. We decided not to do any WhatsApps or emails, to have an afternoon off, and then we’ll go headlong back in tomorrow.
Hopefully with a yes from the government.
Hopefully. It’s possible, and this is what I’m hoping… I rather suspect the government won’t commit itself to one design, nor will it want to have competing designs. We shan’t be competing for the same components in the supply chain. If you want standard ventilator parts then if you have two designs that are sort of similar, using the same stuff, then there’ll be a bottleneck. Our design, even if you do it in parallel with another, won’t compete with it, because we’re just not using anything like the components they would use.
We are ready to go, we are simple, and we can knock it out very quickly and could just plug the surge in the next two weeks. By that time it would give a bit more lead time to anyone who wants to make a more sophisticated, conventional ventilator. But if we just relied on conventional ventilator design, there’d be a huge number of deaths before they’re delivered.
I think it might be sensible, if I was the government, to say these guys have their simple design that they can knock out in a week, and in two or three weeks we should have something a bit smarter coming online. And even if we haven’t got anything a bit smarter, this is still good enough. I’m rather hoping their logic will work like that.
